Additive metallic manufacturing will be achieved in a variety of methods, however the thought is usually the identical: you run a giant printer that deposits molten metallic in layers onto a substrate that then fuse collectively right into a stable form. By printing from the bottom up, you may create shapes which might be not possible to make with conventional subtractive manufacturing, and whereas it is too sluggish and fiddly for mass manufacture, it is an extremely quick and efficient method for small-run elements and speedy prototyping.
Lots of as we speak's metal-printing programs use lasers to warmth and soften powdered metallic feedstocks. Rosotics founder and CEO Christian LaRosa says there are a selection of issues inherent in laser programs. Firstly, these powdered metallic feedstocks are costly and ceaselessly hazardous – for instance, powdered titanium is explosive. Secondly, the lasers are an inefficient means by which to translate energy into warmth. Massive-scale laser-based programs can require particular power provide programs.
Thirdly, they are often harmful – even a mirrored beam of that type of energy will be sufficient to blind somebody if it hits them immediately within the eye. And fourthly, elements created by these strategies sometimes should be heat-treated afterwards, that means you can solely print elements as huge because the oven you may bake them in afterwards.
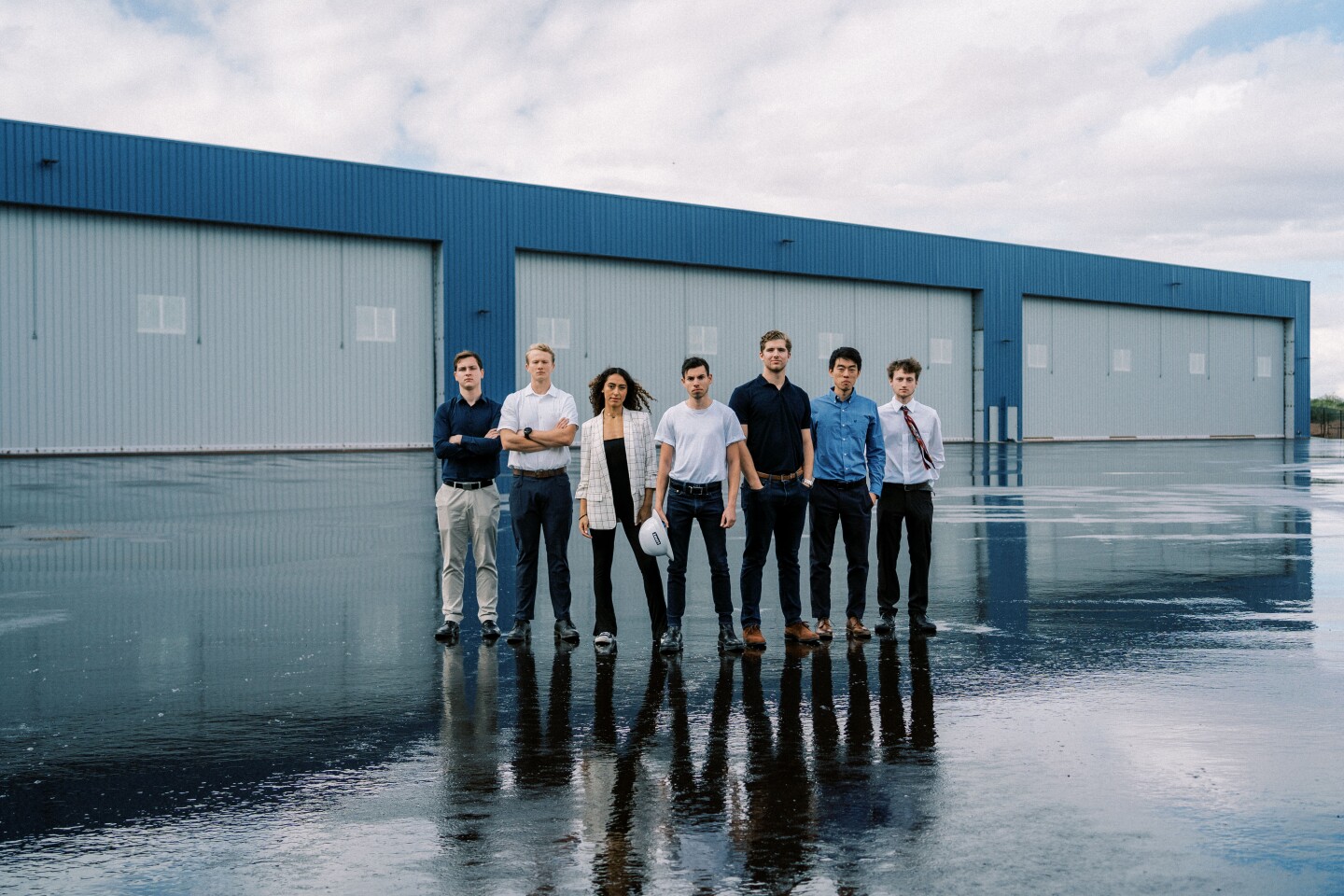
LaRosa says he is give you an alternate that addresses all these points, and opens the door for affordable, simple and quick printing of giant metallic elements, sufficiently big for structural use in plane and rockets. Rosotics has designed, constructed and examined a brand new kind of metallic 3D printing head, known as the Mantis, that delivers warmth to the metallic extremely effectively, via induction.
"It is a very pure method of 3D printing a metallic, in my view," LaRosa tells us over a video name. "You generate an electromagnetic discipline from a coil, and any ferromagnetic metallic that passes via that discipline is heated inductively, by the eddy currents you are inducing within the metallic. We take away the laser from the method; we merely feed wire via a nozzle, and inductively warmth it because it's passing via. We name it Speedy Induction Printing, or RIP. It will get you to the identical objective with far much less power loss."
How rather more environment friendly is the method? "Effectivity in a laser primarily based course of is, in some ways, fairly abysmal," says LaRosa. "It is an optical technique of transferring warmth. Transferring to an induction course of, you are ramping up the effectivity fairly closely. In comparison with directed power deposition, the laser-based wire-feed strategy, we're 30-50% extra environment friendly on the entire power spent. In comparison with others, it may be almost an order of magnitude."
The feedstock would not should be ferromagnetic, both. "Aluminum was a giant goal for us to hit, as a result of it varieties the idea for lots of structural elements in aerospace, and it isn't magnetic within the slightest," says LaRosa. "So we discovered distinctive methods to inductively warmth that feedstock that make the most of breakthrough approaches in metallurgical science. You'll be able to inductively warmth a jacket of inductive materials, or you may have the goal feedstock touring via an inductively heated channel that delivers warmth via bodily contact."
This opens the method as much as a variety of metals. The corporate has examined extensively with metal and aluminum to date, however LaRosa says it ought to be capable to deal with most metals: "From what we have seen, the supplies extensively utilized in aerospace and the niches we're focusing on, it may possibly deal with them fairly comprehensively," he says. "There are probably many supplies that'll push the boundaries, however even then, we have room to alter the method and possibly deal with these as effectively. Titanium is a fairly workable materials, however there's a variety of others we're analyzing. One of the speedy ones is cupronickel, which has excellent mechanical efficiency in sure makes use of. However general, the method performs pretty effectively with any materials that is commercially obtainable in wire type."
The printer at the moment handles wires between 1-10 mm in diameter, however LaRosa says that may simply scale upwards if needed, just by widening the nozzles.
Rosotics has constructed a prototype – in appreciable type. "There is a full scale printer prototype behind the wall on my aspect right here," says LaRosa, "that prints to about 26 ft (8 m) in width, and about 20 ft (6.1 m) in peak. That machine is working three heads, every pushing a little bit over 15 kg (33 lb) of metallic an hour. As a system, it is placing down about 50 kg (110 lb) an hour. It is working off a 240-volt outlet such as you'd discover in any typical warehouse atmosphere – in case you have been working a large-scale wire-based laser printer, you'd in all probability be contacting the facility firm to get a much bigger hyperlink to the grid. I believe that speaks volumes; whenever you make the method extra environment friendly, the whole image simplifies.
"Our course of works in open air, too," he continues, "so you do not have to comprise your complete print quantity in a vacuum chamber. And with different laser-based processes, you want to warmth the whole construction uniformly, to cut back the residual stresses the method has induced. We do not have to do this type of an operation post-print. That simplifies the operation even additional. And whenever you get to giant scale, there is likely to be a handful of furnaces for warmth therapy at that dimension in the whole United States."
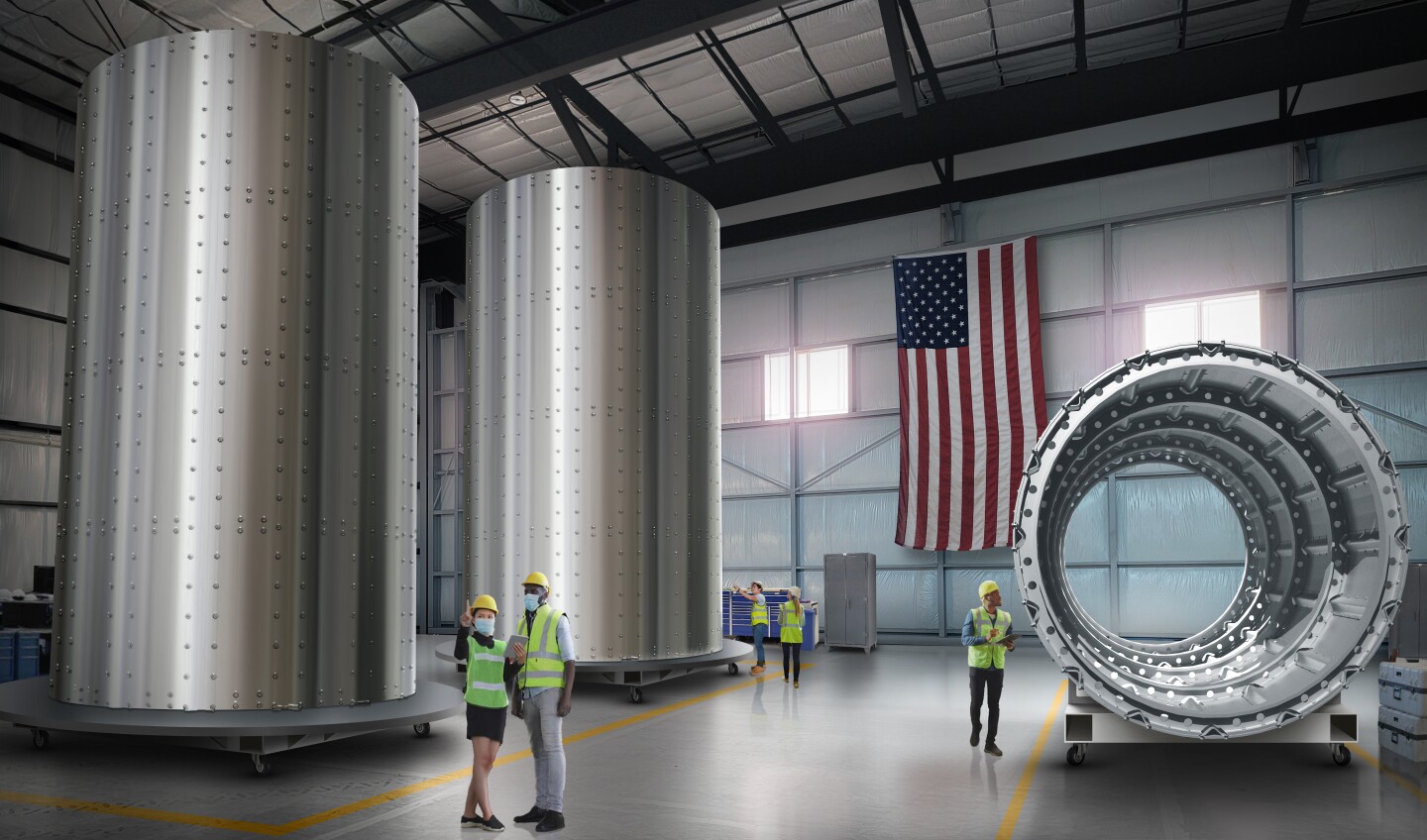
The RIP course of is claimed to make the whole course of a lot sooner and cheaper, and open metallic printing as much as nearly limitless scale. "Numerous the explanation we bought began," says LaRosa, "is that 3D printing has revolutionized manufacturing and the way elements are made – but it surely's restricted by dimension. Heavy trade has been locked out from utilizing 3D printing within the areas you actually wish to be making use of it – actually giant elements made in small numbers. That is why we exist. I used to be a 20, 21-year outdated child working within the design and manufacturing of rocket buildings, and I used to be pained by the truth that we could not use 3D printing at that scale. I am certain might others in aerospace have had the identical feeling.
"I am an engineer by schooling, by coaching and by follow," he says, "I am a founder by necessity – the need to beat this limitation in 3D printing. When it turned obvious that this course of might to that, I could not sleep at night time till it existed. I wasn't totally assured proper off the bat, however as I began pitching it to folks larger and better up the chain, even in NASA's ecosystem, and located that the method would carry out as anticipated, that was the purpose the place I needed to go full time and make this factor a actuality. And day by day now, I am progressively extra humbled, seeing the method – not simply in simulation, however in actuality, doing what we count on it to. We're actually excited to get it onto the marketplace for clients.
"Our system could be very effectively suited to structural functions, say the construction of a rocket, or the construction of a tank," he continues. "Any type of structural half that aerospace would demand, our system can do it. However it's designed to department out to heavy trade at giant. Vitality, marine building, we will serve these functions very effectively."
For something that is bigger than a fridge, this strategy blows any different out of the water. It is only a no-brainer.
Based in 2019, Rosotics closed a US$750,000 funding spherical final November.
"We're funded to the pre-seed stage," says LaRosa, "to get the method confirmed and validated. We have got the platform and the prototype constructed, and we all know with nice confidence what the method can produce. And now we're preparing for the gauntlet: the institution of an meeting line and manufacturing, with its personal challenges when it comes to not simply making the machines work, however effectively constructing them repeatedly in giant volumes. We severely worth vertical integration, and having a modular platform that may mutate over time to fulfill completely different functions. So we're growing an in-house functionality for meeting and manufacturing.
"Now we have a variety of clients which have signed," he continues, "however nothing that we will announce proper right here. Timeframe-wise, we estimate the system will probably be prepared for full-scale deliveries later this yr."
Rosotics as we speak opened up its manufacturing service for certified clients, beginning in October this yr. With a minimal deposit of US$95,000, clients will be capable to run prints in metal or aluminum as much as 30 ft (9.1 m) in diameter, and weighing as much as a number of metric tons. The corporate has additionally introduced its "extremely superior manufacturing campus" will probably be at Falcon Area Airport in Mesa, Arizona.
Notable of their absence at this stage are any pattern prints, but it surely appears potential clients will quickly be capable to see for themselves how effectively this tech handles the standard and precision required in aerospace. We sit up for seeing the way it goes.
Supply: Rosotics
Post a Comment